A good article with some interesting comments and thoughts worth paying attention to about mounting red dot sights ( RDS) to pistols.
Article isn't completely applicable from what read to all manufacturers of red dots or pistols, but gives some good general advice worth listening to and thinking about. Is good general advice from what read.
For example: Torque settings for fasteners can vary between mfg's, but mounting methods are usually similar. Article states fateners at 12 inch pounds, but that is for a particular application. It's usually 12 to 15 inch pounds from what seen for different applications, but settings can and do vary from one to another. A good idea is to check with manufacturer or their website for torque settings for particular application if info isn't included with RDS.
Another important example stated? Just simply cut or machine slide? Just simply drill holes in slide? Are valid reasons stated of doing or planning to and possible solutions for some firearms in article of what to think of and plan for when asking to mill slides or for mounting RDS such as importance of shear strength. That's a biggie. RDS mounting isn't always quite as simple as it may sound or some may think? But, it can be easier with some planning.
www.police1.com
Article isn't completely applicable from what read to all manufacturers of red dots or pistols, but gives some good general advice worth listening to and thinking about. Is good general advice from what read.
For example: Torque settings for fasteners can vary between mfg's, but mounting methods are usually similar. Article states fateners at 12 inch pounds, but that is for a particular application. It's usually 12 to 15 inch pounds from what seen for different applications, but settings can and do vary from one to another. A good idea is to check with manufacturer or their website for torque settings for particular application if info isn't included with RDS.
Another important example stated? Just simply cut or machine slide? Just simply drill holes in slide? Are valid reasons stated of doing or planning to and possible solutions for some firearms in article of what to think of and plan for when asking to mill slides or for mounting RDS such as importance of shear strength. That's a biggie. RDS mounting isn't always quite as simple as it may sound or some may think? But, it can be easier with some planning.
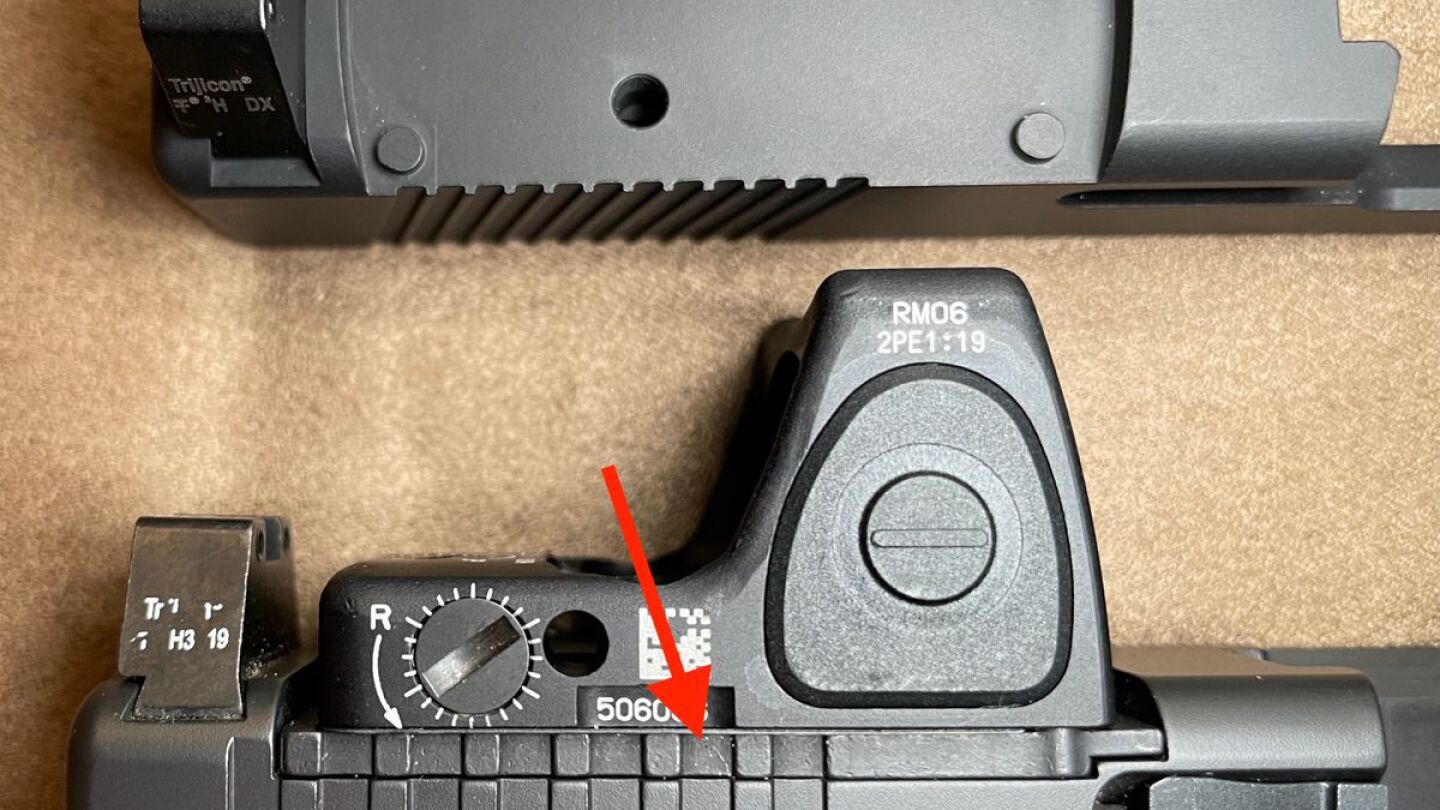
Properly mounting red dot sights
The first step is understanding the forces that act on an RDS
