Behind the Scenes: My Pelican Cases Factory Tour
April 1st, 2024
6 minute read
“Built to Protect” is the motto of Pelican, the company that invented and perfected the all-weather, all-conditions hard case. When gun owners, law enforcement officers, fire and EMS personnel, and the U.S. Military need to transport easily damaged or valuable firearms (and any other equipment), they say “put it in a Pelican”.
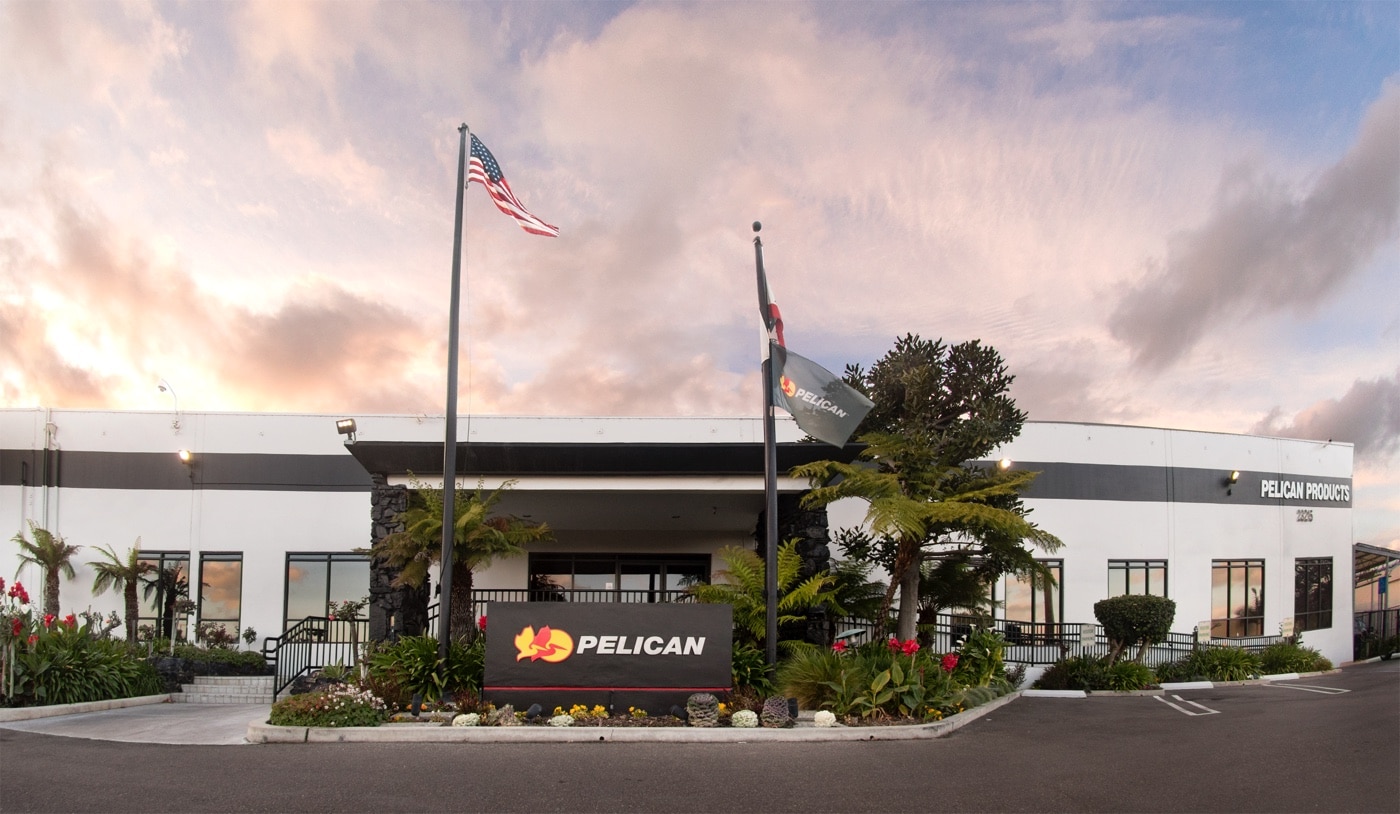
In my experience, the name “Pelican” has become synonymous with an indestructible case that will protect the contents.
In Person
I was recently invited to tour the Pelican factory in Torrance, California with Thomas Van Schoor, Director of Worldwide Manufacturing Engineering, and Jennifer Morse, Marketing Manager. The facility is over 200,000 square feet, with 125,000 of those square feet dedicated to manufacturing. That’s over four acres in total, of which close to three are dedicated to making Pelican Protector, Vault, Air and Personal Utility cases. The Pelican Storm and Cargo cases as well as 20 quart and larger Elite Coolers, are made in So. Deerfield, Massachusetts.
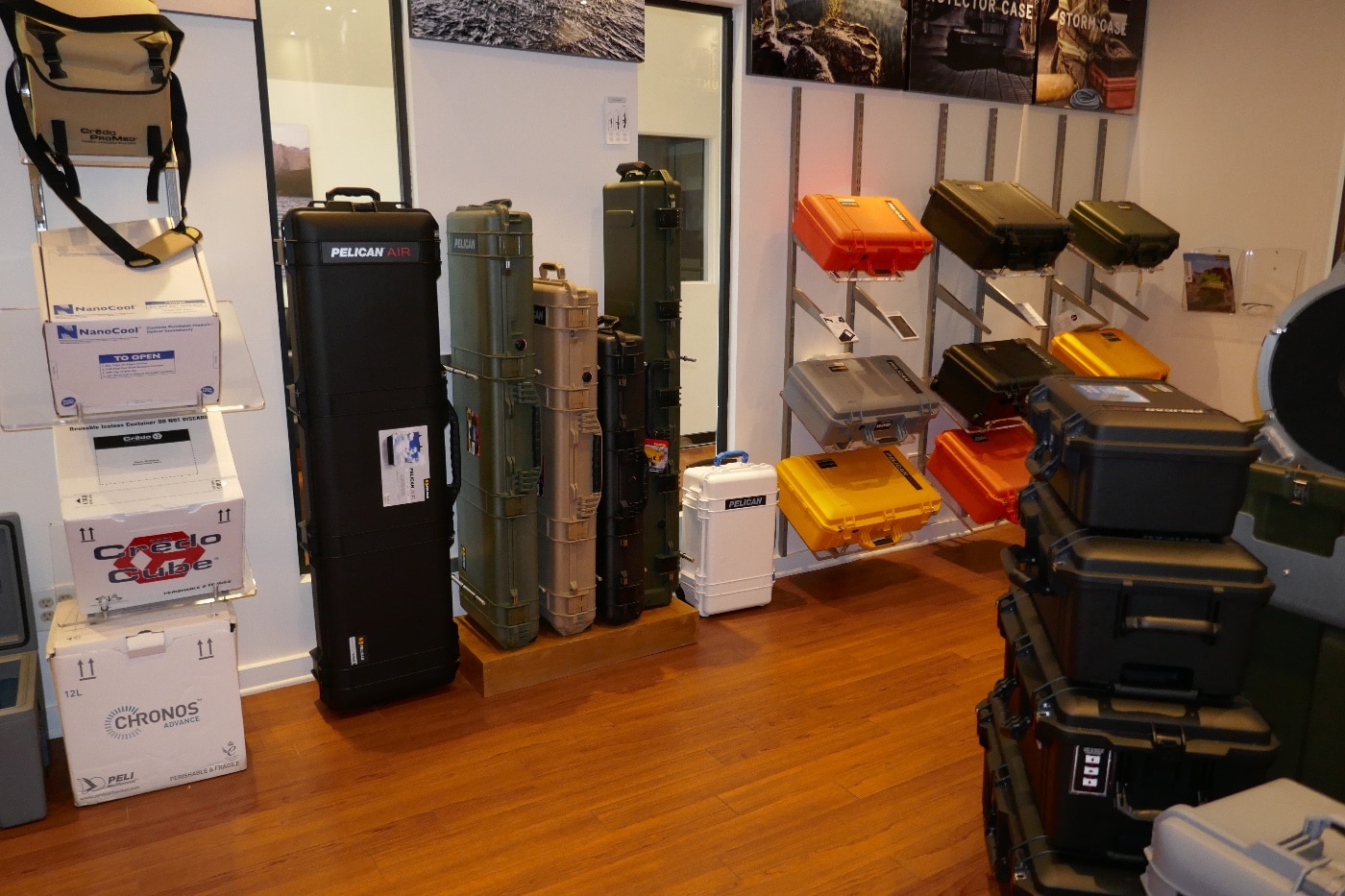
Pelican employs over 1,000 people in the United States, and even more worldwide. The Torrance plant is non-union and has high employee morale from what I saw while there. Many employees have decades of tenure and commensurate collective knowledge. Thomas told me that he has worked for Pelican for more than 28 years.
Each month, an employee is selected as “Employee of the Month” based on outstanding job performance. The chosen employee’s name and photo are posted on the wall. This is a source of pride and motivates all employees to do their very best work. There were lots of smiling faces on that wall.
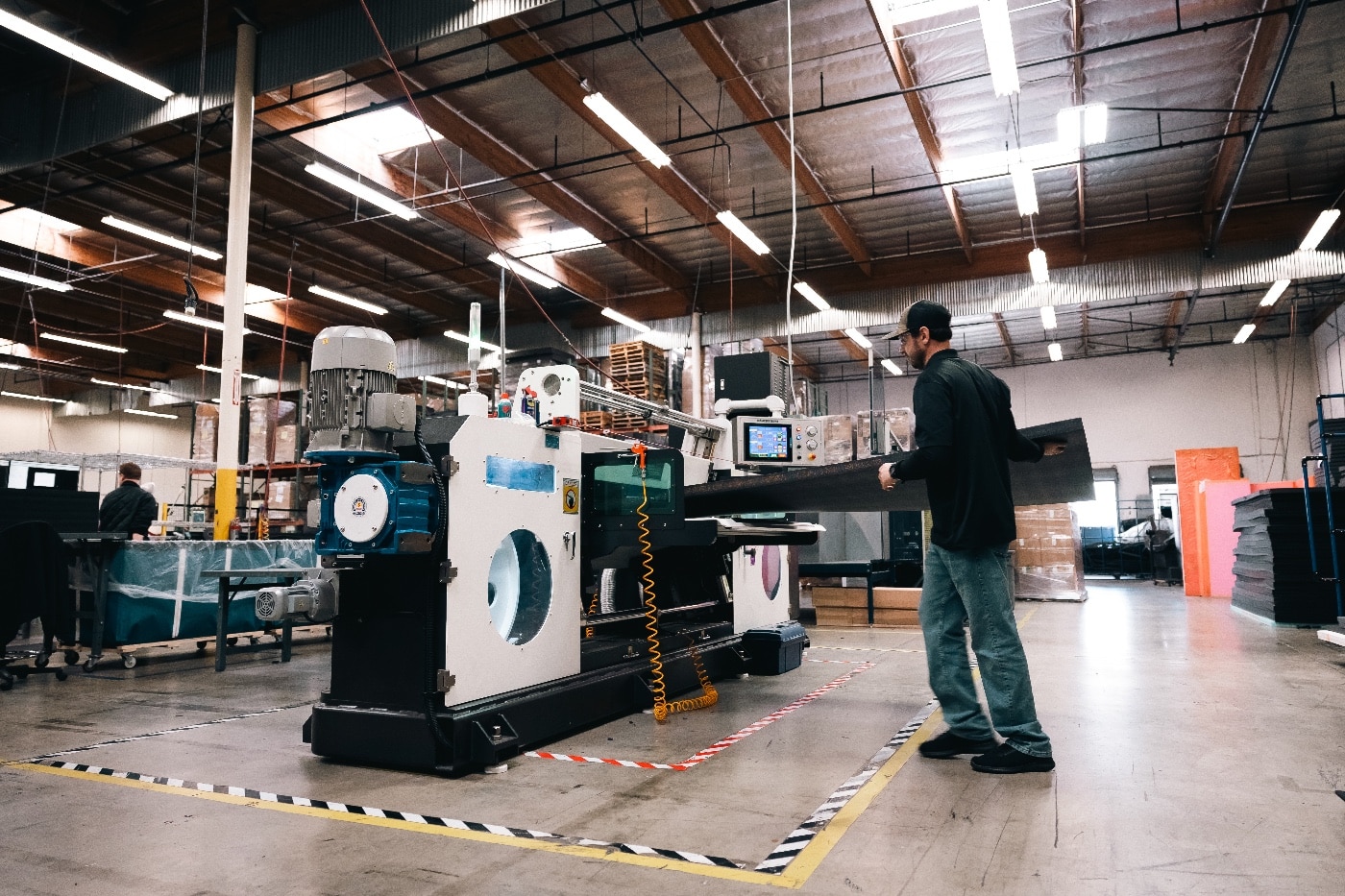
The high morale and work ethic was obvious as I watched workers assemble various Pelican cases. The factory runs three shifts per day, and each shift meets with the next shift to “pass on” anything that happened that might impact production. Each shift has its own meeting during the day to discuss anything that is not running properly or any problems that were addressed. The company places a high value on producing a quality product.
The Foundation
Pelican was founded in a garage in Torrance, California by a man named Dave Parker. The history resembles many other successful American manufacturers. The company has grown exponentially over the past 45 years and now operates in 32 countries with eight manufacturing plants — two of these are in America as well as a custom case center and other U.S. facilities. The company also has factories in Germany, Australia, China and the United Kingdom.
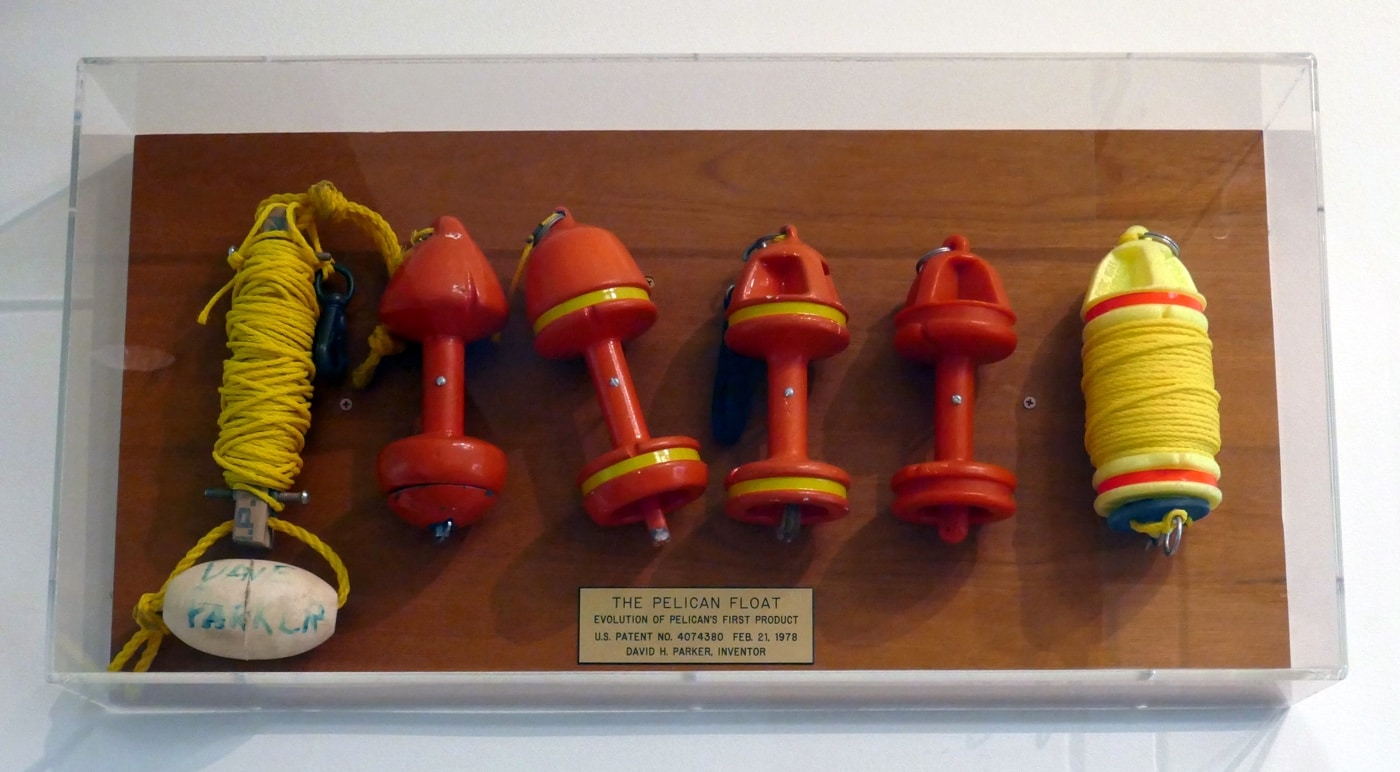
What started the whole thing was the fact Mr. Parker was a diver and needed a device to use as a marker when divers were underwater. He invented and made such a device — and that first Pelican product helped to save lives. Next came a first aid kit — also for divers. The company grew from there and started making waterproof cases. Once Pelican perfected the waterproof case, it was easy to add different shapes and sizes. Thomas told me that Pelican works hard to stay consistent with the founding principles of the company.
The Pelican factory is a blend of high-tech automated injection molding machines and robots along with skilled manual labor to assemble handles, hinges, wheels, rubber gaskets and latches that are made separately from the cases. The machines mold both the top and bottom of the case at the same time. The two halves of the molded case are then picked up by a robot and placed on a conveyor belt, which moves the case to the workers who will assemble it.
The case top and bottom are placed in a jig that holds them in position while a machine drills holes for the handles, hinges, wheels and latches. The wheels are installed, foam is added — as are stainless steel hinge pins, latches, an “O” ring gasket and an automatic pressure release valve. The small parts are installed by hand. The case is then stacked for boxing. Pelican keeps on hand a healthy supply of latches, hinges, and wheels that are stored in bins that are moved to the places where they will be assembled onto cases as they are needed.
The 22 injection molding machines in Torrance exert anywhere from 85 to 3,000 tons of pressure — depending on what product is being manufactured. Several different molds are moved in and out of these large machines depending on what product is being made.
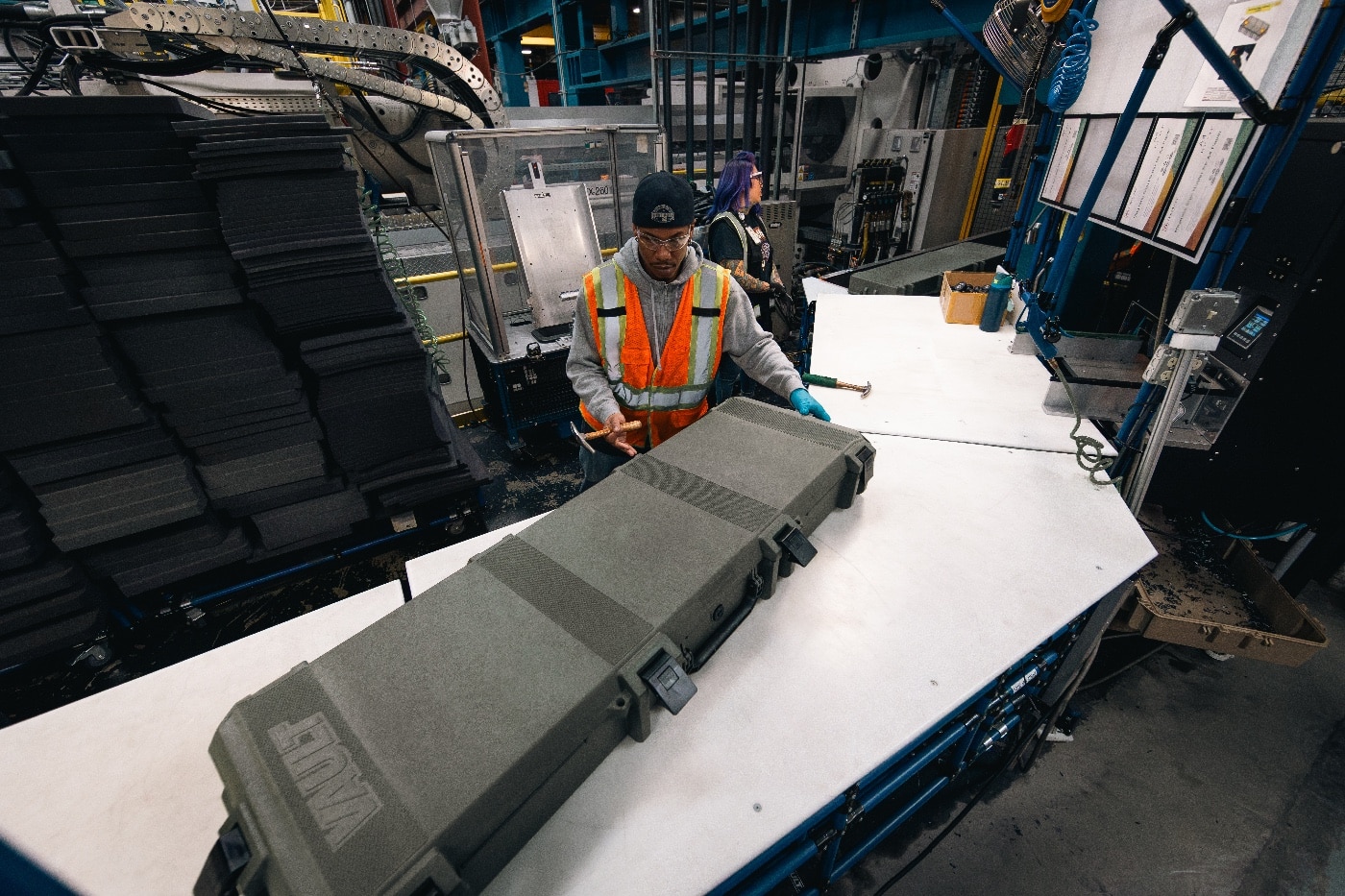
What I found unique is that the machines have names. Some male, some female, including names such as Arline, Thor, Colossus, Titan, Hercules and King Kong. This certainly does make the factory floor interesting. The average life span of an injection molding machine is 15 to 20 years. While I was visiting, I was shown an area where a new machine was going to be installed to replace an older, aging unit.
Where It Counts
There are rare instances when a case does not meet Pelican’s strict quality specifications. Either the color or dimensions are just not right or a worker found something else to be wrong. Those cases are never sold. The case is added to a stack of cases to be “reground”. In other words, the case is pulverized so that the plastic resin can be reused.
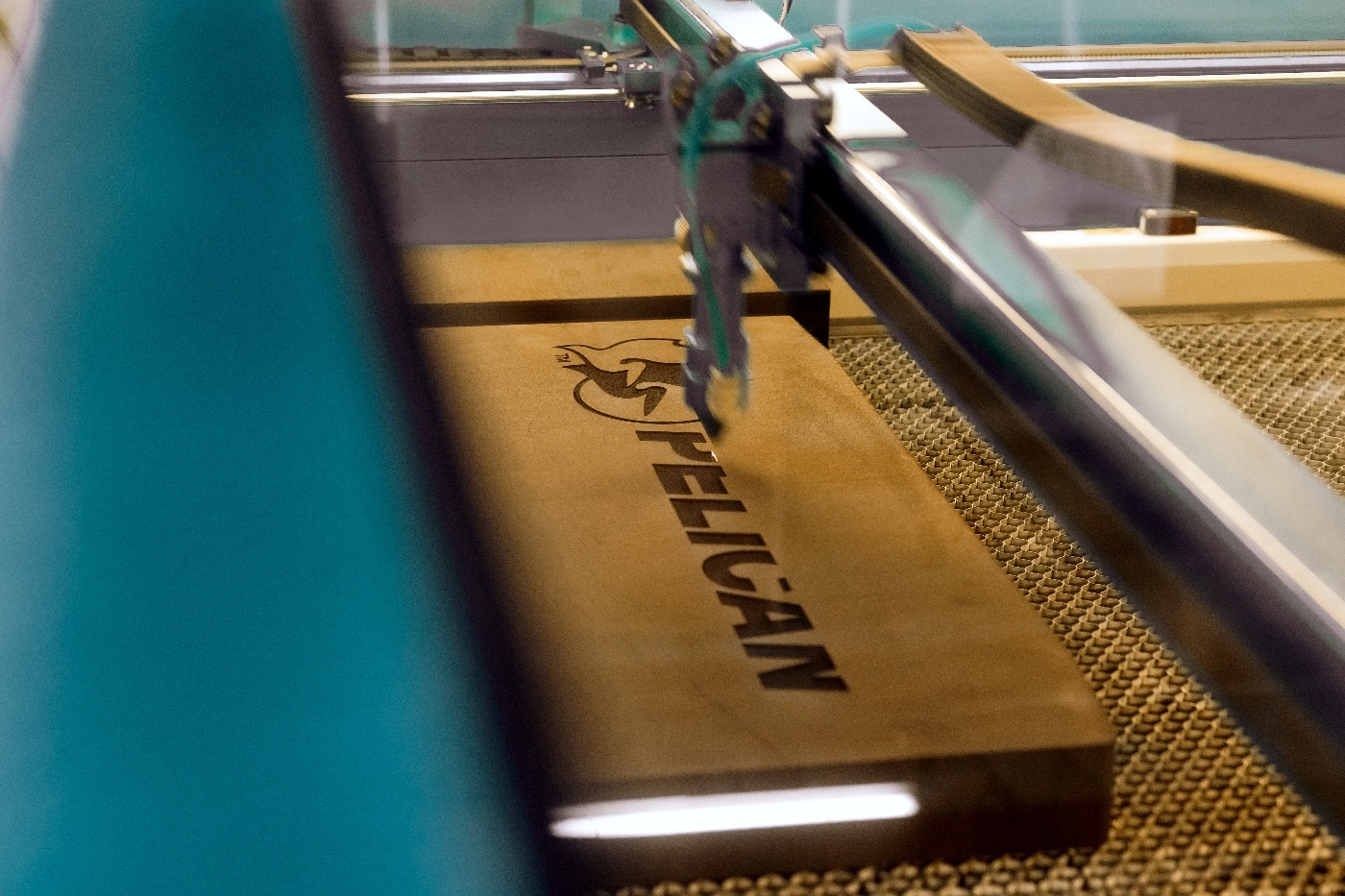
There is little waste in the plant. Outside, there are four silos to hold virgin, reground, foam and color resin. These silos feed the machines in the plant through pipes and tubes.
To keep things running smoothly, Pelican uses 21st century software to make sure that all machinery in the factory is maintained according to a strict schedule. All preventive maintenance is planned so that even if a machine is not making cases, production flow is not disrupted. Pelican has several milling machines and other equipment and tools that are used to fabricate parts as needed.
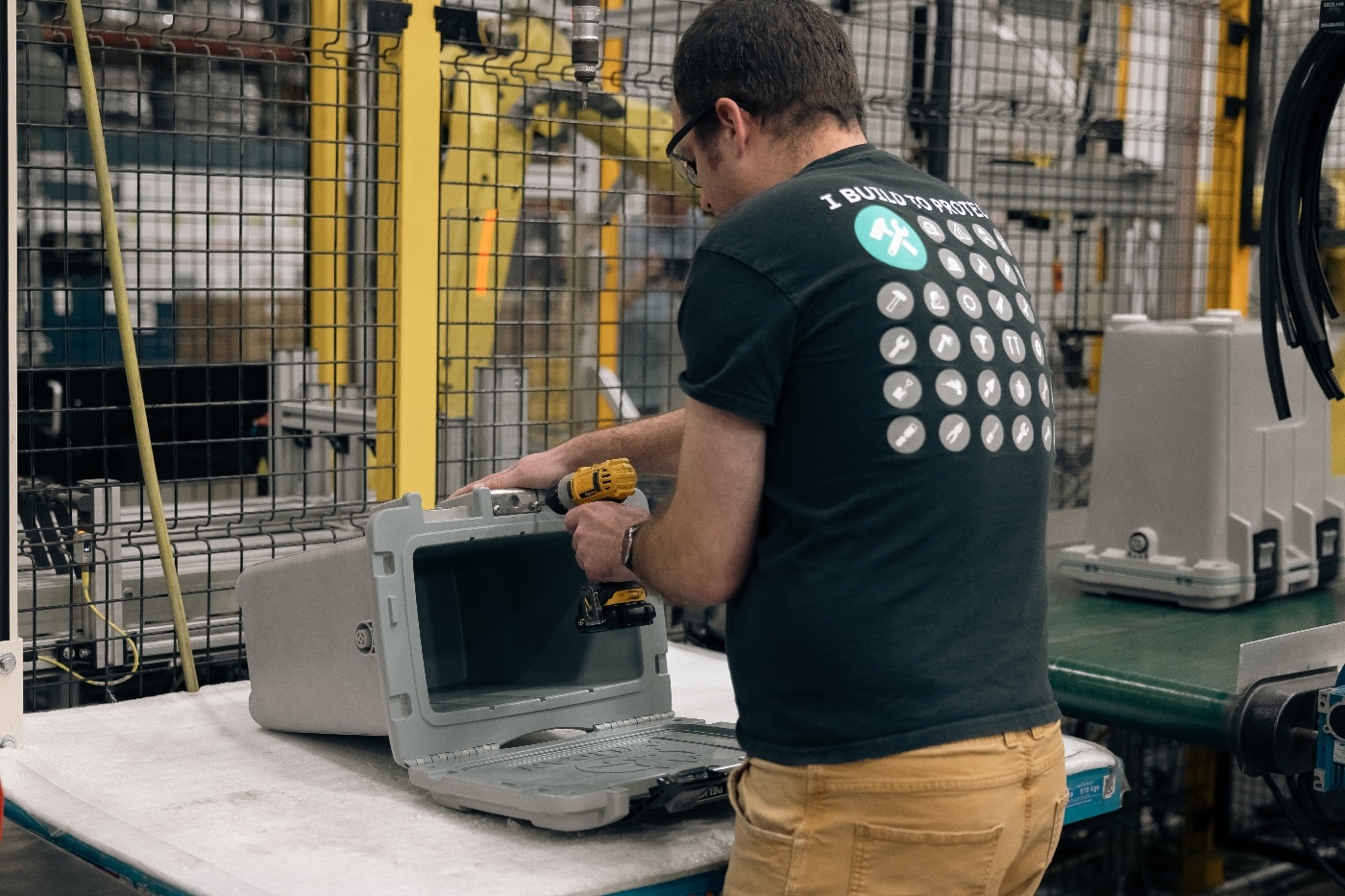
The company is able to make special production runs of custom colors. For example, if your gun club or shooting team wants a Pelican cooler or case made in a special color scheme, and is willing to purchase in bulk, (as little as 25 for Elite wheeled coolers), Pelican will happily produce a run for you.
As you probably know, cutting foam, solid or Pick N Pluck™, can be tedious and frustrating for end users. With effort, patience and skill these types of foam can be configured to safely hold equipment in place. But a perfect solution is difficult to obtain. Pelican recognized this and now offers a service to pre-cut foam for most cases aptly named, Pelican Foam. This service is available for most Pelican Protector, Storm, Air and Vault cases.
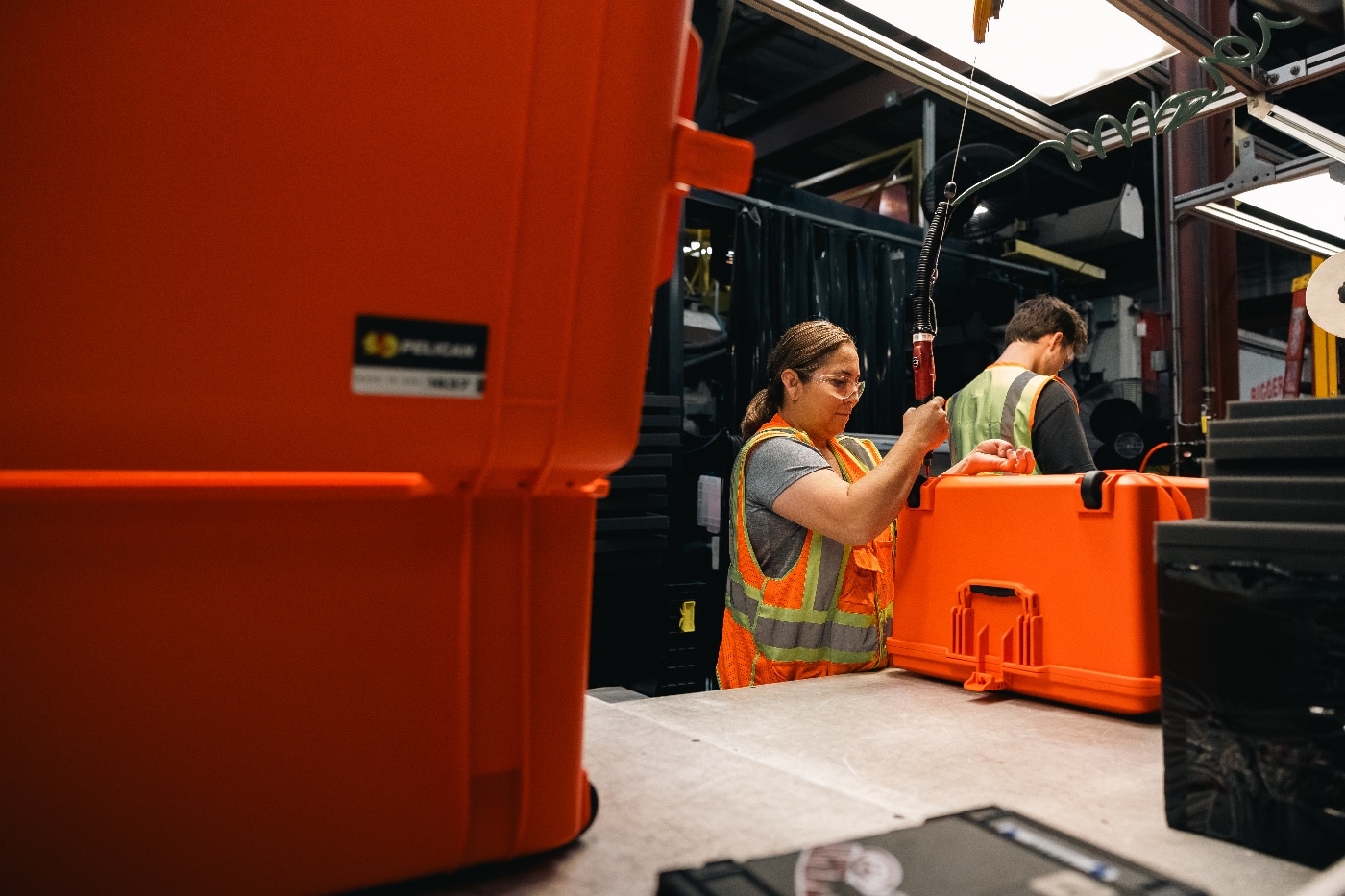
A customer can buy a case of their choosing, design the interior using an online tool or even upload a photo of their items and the experts at Pelican Foam will do the rest. Customers can also purchase just cut foam for a Pelican case. This option allows customers to purchase one case and configure it to carry many different firearms and accessories by purchasing additional pre-cut foam inserts.
In addition to hard cases, cargo cases and coolers, the company makes flashlights as well as biothermal cases (both single use and reusable) that were used to ship cold antibodies during the pandemic.
Conclusion
Pelican’s history is one of phenomenal growth through innovation. Pelican’s story truly shows how great American manufacturing can be. I have been traveling with guns secured in Pelican cases for decades; after my factory tour, I can comfortably say that quality is priceless. I left the factory more certain than ever of that fact.
Editor’s Note: Please be sure to check out The Armory Life Forum, where you can comment about our daily articles, as well as just talk guns and gear. Click the “Go To Forum Thread” link below to jump in!